博硕涂装解决方案
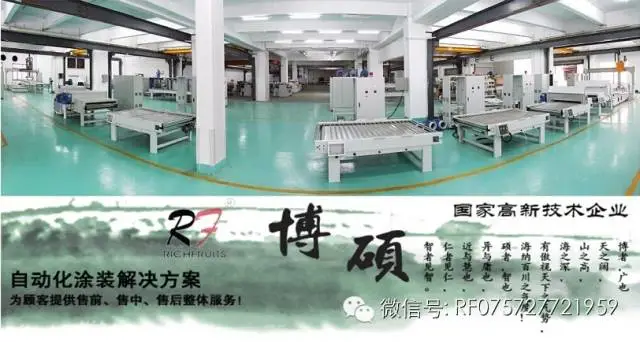
1 木器家具涂料在涂料工业中的地位
很多国家均居工业涂料之首,其产量一般占其本国涂料总量的10%左右。
1.1 经济效益可观
1.1.1 产量
1)国外
美国涂料产量长期居全球首位,其产量在2006年达到顶峰,总产值达208.7亿美元,其中木器涂料产值29.8亿美元,占涂料总产值的14%。在金融危机发生之前,美国的木器涂料产业呈增长的态势,年平均增长率为3%~5%。2005年欧洲工业涂料总产量为290万t,其中木器涂料占15%。预测2015年欧洲木器涂料产值将达到14.7亿欧元,比2003年增长22%,其中水性木器涂料产值要达到3.3亿欧元,比2003年增长57.14%。2006~2008年,亚太地区木器涂料产业年增长率最高达14.9%,高于世界木器涂料平均增长率数倍。2008年中国木器涂料占亚太地区木器涂料市场的73%,产量仅少于当时的美国,居全球第二位(2009年跃居世界第一)。
2)国内
2006~2010年国内木器涂料产量占全国涂料总产量均在10%,2011年后,木器涂料在涂料总量中占比降至8%以下,说明木器涂料增速开始低于涂料总量的增速(表1)。在国内涂料品种结构中,除建筑涂料外,木器涂料占工业涂料的首位,排在汽车、船舶、粉末等工业涂料之前(表2)。从产值上看,据家具协会统计,2013年国内家具行业产值已达6 462.75亿元(实现利润403.88亿元),仅次于房地产、汽车、食品,列国内第四位,并连续5年居世界第一。在家具产值中,木器家具产值4 118.13亿元,金属家具1 270.9亿元,其他家具864.13亿元,说明木器涂料的重要性。
1.1.2 高质量木器涂料是木器家具出口的重要支撑
1)国外
出口家具的美丽外观和耐用的质量靠高质量涂料装饰与保护。美国在2007年以前是家具出口大国,木器家具产量的一半出口到亚洲、欧洲和其他地区,一半为自用。欧洲木器家具出口量大,仅意大利在2007年家具出口约100亿美元。
2)国内
中国是家具出口大国,2013年,我国累计出口家具531.01亿美元,同比增长6.30%, 2013年国内家具累计进口25.70亿美元,同比增长10.11%。对外贸易顺差进一步增加至505.31亿美元,同比增长11.0%。国内木器家具产值和利润均占整个家具的61%以上,不考虑木器涂料用于塑料、竹、藤、金属家具和其他家具,也能说明高质量木器涂料对整个家具出口起重大支撑作用。
1.1.3 木器涂料污染性大小与人民健康密切相关
木器涂料主要应用于家具、地板和室内装饰装修,直接与人接触,其中含VOC高低、有毒有害成分多少,关乎居家生活人们健康,受到国内外重视,提高了政府和社会对木器涂料的重视程度,也是说明木器涂料的重要性。
2 木器家具用涂料产品结构
2.1 国外
木器用涂料品种发展至今,尽管溶剂型涂料仍占主要部分,但水性、UV固化涂料在国外所占份额逐步增加。聚氨酯(PU)、硝基(NC)、聚酯(含醇酸)、酸固化(AC)等产品属溶剂型涂料;水性涂料(W-B)中包括醇酸乳液、丙烯酸乳液、聚氨酯水分散体,以及它们的复合体。紫外光(UV)固化涂料包括不饱和聚酯、丙烯酸及其改性的聚酯、环氧、聚氨酯等品种。2006年统计,全球木器用涂料中水性涂料和UV固化涂料占10%左右,不饱和聚酯(UPE)占8%,其余为溶剂型涂料。
2.2 国内
尽管国内各方面都在宣传、强调重视水性木器用涂料,但进展不尽人意,目前木器用涂料仍以溶剂型为主,水性木器涂料只占4.5%左右。
3 发展水性涂料为代表的低污染型木器涂料势在必行
3.1 木器涂料产业面临环保经济压力和挑战
3.1.1 国外
以欧洲为代表说明对木器涂料的环保法规日趋严格。2002年,欧盟颁布了包括不同木器涂料品种的VOCs限值法令,溶剂型木器涂料限值为400 g/L,水性木器涂料限值40 g/L(2010年),这些限值是较严的。
3.1.2 国内
1)已颁布的相关强制性国家标准
国内对室内装饰装修有2个强制性标准:GB 18581和GB 18582,前者对室内装饰装修用的醇酸、硝基、聚氨酯3种溶剂型涂料VOCs限值作了规定,后者对室内水性建筑涂料VOCs限值作了规定,但标准较宽。
2)正在酝酿研究制定工业涂料涂装VOC排放限值强制性标准
“我国涂料产品与涂装行业挥发性有机物排放特征及控制对策研究”项目,国家环保部已立项,由环保部环境规划院牵头,中国涂料协会等4个单位参加,以木器涂料涂装、汽车涂料涂装等7个工业涂装行业为重点,调查研究VOC排放和控制技术情况,是制定整个工业涂料与涂装(包括木器涂料)工艺中VOC排放限值的强制性标准的前期工作,要逐步和国际接轨。
3)国家要开征溶剂型涂料消费税
近日,国家环保部、财政部和国家税务总局有关部门为鼓励发展环境友好型涂料逐步取代溶剂型涂料,决定对溶剂型涂料开征消费税。就此召开了几次座谈会,有中国涂料协会负责人、专家和重点涂料企业代表参加,对如何征收溶剂型涂料的消费税听取意见。这对促进水性等低污染涂料发展有积极意义,但从短期看,会增加涂料产品成本,降低利润,这对于成本不断提高的涂料行业,无疑将是新增加的一种压力。
3.2 水性木器涂料发展现状
3.2.1 木器用水性醇酸树脂涂料
醇酸树脂原料来源广泛,有的是可再生资源,综合性能好,成为涂料行业中骨干品种。溶剂型醇酸树脂涂料曾是木器涂料的主流产品。随着聚氨酯、丙烯酸等在木器涂料中得到推广应用,醇酸树脂逐步退居木器涂料的次位。
国外在20世纪50年代中后期开始水性醇酸树脂的研究并实现工业化。国内开始研究水性醇酸树脂比国外晚10多年。方法是合成较高酸值的醇酸树脂,后用氨水或脂肪胺中和形成盐基型树脂,先溶于助溶剂(亲水亲油性,如醇醚类溶剂)中,然后加水稀释,成为水可稀释的分散型醇酸树脂。水稀释型醇酸树脂可以获得和溶剂型醇酸树脂相近的性能,如配方设计不当,在贮存中涂膜干燥速度往往变慢成为制约其发展的技术关键问题。为使树脂能较好地溶于醇醚等助溶剂中并能经水稀释后稳定,树脂相对分子质量不宜过大。而醇酸树脂是以多元醇、多元酸酯化的酯键为主链,在水介质中,弱酸弱碱(体系中是存在的)催化易水解而降解,在贮存中树脂黏度逐渐降低,所以干性下降。现在许多公司致力于改变醇酸树脂分子结构,优化催干剂体系,改善其干性,有一定的效果。
醇酸树脂是由酯化缩合逐步增长成线形聚合物,酯化反应是可逆反应,必须将反应水不断引出体系外,才可使反应继续进行,故醇酸树脂不可能在水介质中乳化聚合。另一种制法是先用溶剂法合成醇酸树脂,然后进行乳化,即后乳化(也称外乳化)工艺。这是国外醇酸树脂水性化的重要技术路线。近几年国内一些单位也在开展这方面的研发,使用后乳化工艺制成水分散型醇酸树脂,达到溶剂型醇酸树脂涂料的综合性能,贮存稳定性好,正争取用于中高档木器涂装。至于有的公司在溶剂型醇酸树脂施工前,加一种两亲型(既亲水又亲油)乳化剂,加水(10%~20%)搅拌乳化分散后施工,虽能节省溶剂,降低成本,但在性能上要大打折扣,只能用于低档涂装,当然也算不上水性醇酸树脂涂料。
醇酸-丙烯酸细乳液杂化聚合水性木器涂料。前已叙述,醇酸乳液具有对木质底材渗透性强、附着力好、光泽高等优点,但干燥时间较长;丙烯酸乳液干燥快、保光性好。采取杂化(hybrid)改性技术可以结合二者的优点。
过去采用常规乳化方法制备醇酸-丙烯酸酯杂化乳液,其分散相中珠滴尺寸一般在10 ~ 100 μm,含表面活性剂;微乳液(microemulsion)分散相的珠滴尺寸在10 ~ 100 nm,采用表面活性剂和助表面活性剂;而小粒子乳液(细乳液miniemulsion)分散相珠滴尺寸在100 ~ 400 nm,含有表面活性剂和助表面活性剂混合物。油脂、醇酸树脂-丙烯酸细乳液杂化工艺是其中的重要进展,大大提高了杂化乳液的贮存稳定性,减少VOC。
一种方法是用氢过氧化油(如氢过氧化葵花籽油)作引发剂,在氧化还原体系存在下,醇酸树脂对丙烯酸酯聚合物起助溶剂作用,减少VOC。杂化体涂膜先进行类似于丙烯酸乳液的干燥,随后自动氧化交联,涂膜干燥后外观透明,性能好。
另一种方法是在醇酸树脂存在下,丙烯酸单体(甲基丙烯酸甲酯、丙烯酸丁酯和丙烯酸)进行细乳液共聚制杂化体。除按要求添加表面活性剂外,还添加少量聚甲基丙烯酸甲酯(PMMA)作为助表面活性剂。分析证实,大约有70%的聚丙烯酸酯可接枝到醇酸树脂分子上;醇酸树脂分子在聚合反应后仍保留70% ~ 80%的双键,保证涂膜在气干中起作用。
杂化乳液配制成涂料(清漆),施涂在木材和金属表面上,干性、硬度和附着力显示了较好结果。油脂、醇酸-丙烯酸杂化乳液涂料的制备技术,以及在木器涂装中应用,国外已接近工业推广水平。近年来国内也有类似的研究。
另外,氨酯油和丙烯酸进行细乳液杂化改性,用于木器涂装,也有较好效果。
3.2.2 木器用水性丙烯酸树脂涂料
(甲基)��烯酸及酯单体和乙烯类单体乳化聚合成乳液树脂早已工业化、商品化,已成为建筑乳胶涂料的主流成膜物产品。由于水性丙烯酸乳液制成的工业涂料涂膜具有许多优点,如耐候性好、不易泛黄、硬度高、光泽好,逐步形成水性工业涂料中的主力军。但水性丙烯酸木器涂料的研发与推广,国内起步较晚。涂料企业和一些高校正投入力量进行研发与应用推广工作,核壳型乳液聚合技术、自交联技术、新单体新助剂改性、用聚氨酯或醇酸杂化改性、无皂乳液聚合等技术和新品种,有的是成熟的实验室成果,有的正在工业化推广。要使水性丙烯酸树脂涂料在木器涂料中发挥像在建筑乳胶涂料中那样举足轻重的作用,还要作极大努力。
(甲基)丙烯酸酯乳液树脂合成和应用虽然很普遍,但不能直接移植于木器涂料,因常规乳液聚合法获得的树脂乳液,其乳液粒子属微米级,涂膜具多孔性,光泽低,不适合木器涂装。北京化工大学李效玉教授以丙烯酸酯为主要单体,配以多种功能单体,通过乳液聚合方法合成出具有多层核壳结构、纳米化的丙烯酸系共聚物乳液,乳液粒子的粒径<100 nm,制成木器涂料,具有耐水性好、硬度高、涂膜丰满度好、耐候性佳等优良性能,在木器面漆、底漆、UV固化涂料中正在广泛推广应用,进行工业化考验[7]。
3.2.3 木器用水性聚氨酯涂料
溶剂型聚氨酯涂料已占国内木器涂料近68%,涂膜性能优良,但使用溶剂量大,发展水性聚氨酯涂料是重要方向。最先发展的是水性聚氨酯分散体(PUD),即单组分水性聚氨酯分散体。10年来,世界PUD保持6%以上的年均增速。据统计,2010年全球PUD市场消费量达37.5万t。世界PUD消费市场的一个重大变化是从主要作皮革涂饰剂转为木材等涂装,用于木器涂装的PUD已占22%,超过了皮革涂饰剂的用量(只占17%)。我国PUD的研究始于20世纪80年代,安徽大学、中昊北方涂料研究设计院有限公司等单位是研发这个品种的先行者,曾列为国家“七五”科技攻关项目,主要用于皮革涂饰剂,在达到工业化程度后,年均增长率超过8%。2010年国内PUD消费量突破11.8万t,消费领域也正由皮革涂饰剂转向木器涂料(占PUD用量的8%)、胶黏剂、手套浸胶、汽车涂料等市场。
单组分水性聚氨酯的木器涂料具有高强度、耐磨损、低温成膜性和柔韧性佳等优点,但因是热塑性树脂,涂膜存在硬度低、丰满度差、成膜初期回黏性差、抗沾污性能低、底漆附着力差、渗色、“胀筋”等不足。国内外对PUD进行了系列改性。一种方法是预交联改性,在聚氨酯制备过程中加入三元醇、用三元胺扩链剂、添加异氰酸酯三聚体等。另外改性方法是用其他的化学单体或预聚物改性,主要有环氧、丙烯酸、有机硅、纳米材料、超支化树脂、可再生资源等改性。
在诸多改进PUD性能的技术路线中,最重要的是丙烯酸酯类的改性。丙烯酸改性水性聚氨酯涂料的方法有物理共混、核-壳聚合、用双键共聚、互穿网络等,都得到不同程度的成功,而互穿网络的改性的效果明显。丙烯酸酯和聚氨酯2种乳液以分子互相渗透,然后进行反应,形成高分子互穿网络的PUA复合乳液,能明显改进PUD的硬度、耐水性等性能。
水性双组分PU木器涂料国内外研究均有发展。羟基乳液与带—NCO基团的固化剂分装,施工前将二者充分混合均匀涂装,羟基组分对固化剂组分起乳化分散作用。涂膜具有优异抗性和较为满意的硬度,整个性能达到溶剂型PU涂料。主要不足是固化剂容易与水反应生成各种副产物,导致漆料活化期缩短、理化性能下降、起泡等不良现象,同时还存在成本昂贵等制约因素。
4 水性木器涂料发展一些新动向
水性木器涂料最大的优点是VOC含量低,主要用水作介质,节省有机溶剂,是省资源(也省能源)的环境友好型品种。生产与应用中可减少火灾危险。水性木器涂料在使用中也暴露了一些不足,由于水的蒸发热较高,挥发速度较慢,影响干燥速度。成膜助剂的低挥发性也减慢了涂膜的干率。
涂膜干燥慢,在工厂涂装时延长了涂装件的待干时间,增加停放场地。涂膜耐化学药品性、硬度等性能逊于同类溶剂型涂料。施工过程对空气相对湿度和温度的敏感性高于同类溶剂型涂料。
针对水性木器涂料现状,其发展方向是改进性能使其达到和超过同类溶剂型涂料,开发可再生原料来源,配套发展涂装工艺,优化产品性价比。下面简介国内外改进水性木器涂料的一些新动向。
4.1 紫外光(UV)固化水性木器涂料
UV固化涂料含VOC低,属环境友好型涂料,生产效率高,2007年以前UV固化涂料全球每年以9%左右的速度增长,UV固化木器涂料产量占整个UV固化涂料产量的1/4左右。
UV固化水性木器涂料是近年来发展的新技术,和UV固化溶剂型木器涂料相比的突出优点是不用有机稀释剂,可使VOC趋向零。国内相当多的UV固化涂料品种中有机溶剂量逐步增多,有的高达60%,已属高污染的涂料品种。
由于水的蒸发热较大,涂料施涂后,在UV固化前要经过烘炉,在70 ℃下烘5~10 min,蒸发湿膜中的水分,然后经UV固化,涂膜可以干透,达到高硬度,是水性木器涂料的一个重要发展方向。
UV固化水性木器涂料先开发丙烯酸系水性涂料,但UV固化纯丙烯酸酯水性木器涂料的涂膜外观、硬度及耐化学性能往往不理想,要做多种改性。首先是提高不饱和度,即增加聚合物的UV交联活性,其次要用聚氨酯、环氧或聚酯等改性,赋予新的性能。
李效玉、陈松用双烯酸和其他丙烯酸酯单体共聚制取可UV固化的不饱和丙烯酸乳液,目的是提高聚合物的不饱和度。其设想是,双烯酸中一个C C双键(假定是C14 C15)用于聚合,而另一个C C双键(假定是C4 C5)留在聚合物中,增加聚合物的不饱和度,即提高UV固化的交联活性。红外分析结果得到了一定的验证。经过双烯酸用量、光敏剂用量、共聚单体中的软、硬单体配比等因素优化后,所得丙烯酸乳胶树脂配成光固化涂料,UV固化后涂膜铅笔硬度可达3H,附着力(划圈法)0~1级,耐水、耐化学药品、耐磨等性能符合相关标准,人工老化800 h,只轻微变色,无明显龟裂。完全符合木器涂料的要求。
北方涂料院王小军、陈小庆等研制了多重交联UV固化水性聚氨酯木器涂料[14],先用顺酐和多元醇合成聚酯多元醇,在主链上引入双键,即引入UV交联的活性点;第二步加入异氰酸酯、功能性有机硅单体和二羟甲基丙酸,在侧链上引入可水解的硅氧基团,进行常温水解自交联,提高聚合物的预交联密度。加入多官能度的有机胺进行扩链和中和由二羟甲基丙酸引入的羧基,使扩链和水分散同时进行。这样可大幅度提高UV固化前的树脂预交联密度和相对分子质量。选用合适量的光敏剂和高压汞灯进行UV固化,涂膜硬度可达0.8(摆杆)以上,附着力1级(划圈法)、耐水、耐乙醇、耐干热性优良。在UV固化前的涂膜常温放置7 d后,涂膜附着力达到1级(划圈法)、硬度达0.6以上。这种预交联的多重改性所获的水分散体涂料在UV固化前的涂膜即具有较好的性能,可满足一般要求下的木器涂饰,亦适用于局部UV难以照射到的异型材的涂饰。
4.2 纳米材料改性水性木器涂料
纳米材料改性涂料可赋予涂料许多特殊性能,这已为国内外涂料技术界所公认。纳米材料改性木器涂料也可达到不同的目的,有的是赋予水性木器涂料抗菌性能,有的是改进水性木器涂料的硬度和耐水性;有的是为了全面提高水性木器涂料的质量,达到同类溶剂型木器涂料的水平 ;有的是研究提高户外木制品的耐久性。
在改性方法上,有外加无机纳米材料和通过化学合成或溶胶-凝胶技术,目的是在涂膜中引入纳米材料或纳米结构组分,以改进涂膜性能。采用溶胶-凝胶技术在木材表面沉积一薄层涂膜保护木材表面免受光氧化作用,这是近年来的新探索。用异丙醇铝和异丙醇1∶40(物质的量比)先制成透明的异丙醇溶液(AOS),然后和甲基三甲氧基硅烷(MTMOS)和十六烷基三甲氧基硅烷(HDTMOS)配成均匀混合液,作为前驱体,AOS∶MTMOS∶HDTMOS=2∶2∶1(体积比)。然后用浸涂法涂布木材试样板,在样板表面沉积一薄层有机-无机的凝胶膜,在70 ℃下烘干,获得耐候性好的涂层。经过水蒸气吸附、液体水吸附、UV照射等试验证实,涂层不影响底材的木纹显露,获得了很好的抗光氧化、抗变色作用,为户外木器稳定作用提供了一个新的途径。
唐本辉、朱延安等用纳米级的硅溶胶和水性高聚物为成膜物,配合一些助剂制成水性木器透明底漆,具有硬度高、干速快、有较好的初期抗压性、耐水性优、附着力好、打磨性好等优点。硅溶胶是一种无机纳米材料(粒径10.5 nm),可能为水性木器涂料找到一种适用的新的纳米材料。
5 结论和建议
木器涂料用量会不断增加,为应对环保法规日严的压力,扩大水性木器涂料应用势在必行。水性木器漆在欧美一些国家中已占木器家具涂料20%左右,且发展较快,国内应该并一定会迎头赶上。
为克服水性木器涂料质量的一些不足,国内外在乳液杂化改性、可再生资源利用、UV固化水性涂料、纳米材料改性等方面作了大量研究,并取得了可喜的进展,对水性木器涂料加快推广在技术上提供了保证;同时显示出对扩大可再生的油脂原料利用、降低成本的重视。
加强宣传、提高人们对使用水性木器涂料的重大意义的认识,不断改进施工工艺以适应水性木器涂料的使用。同时,国家有关部门和行业协会应加快制定水性木器涂料的技术标准和木器涂料VOC限值标准,促进水性木器涂料更快地推广应用。
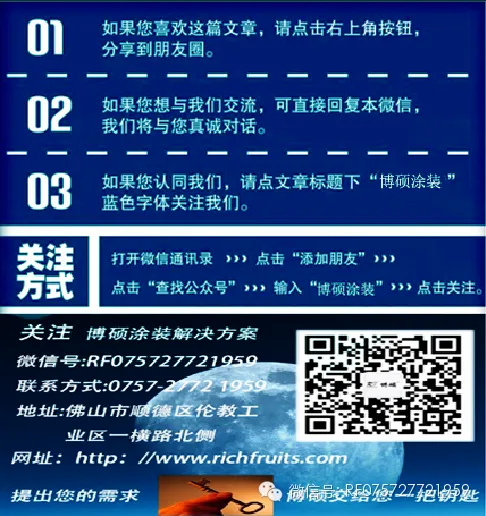